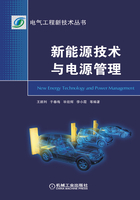
2.3 锂离子电池组的热管理
2.3.1 热管理的必要性
锂离子电池组在快速充放电的过程中会产生大量的热,若散热不及时,会造成电池温度过高、模块间温度分布不均衡的问题。在高寒地区或低温环境下,容易导致电量流失严重、充电缓慢等现象。常见的新能源汽车用电池本质上是将化学能直接转变为电能的电池,电池内部化学反应是否能顺利进行,直接影响着电池的性能。众所周知,温度对化学反应的进行有很大的影响,因此,电池性能在很大程度上受到温度因素的影响。化学反应主要集中在电极和电解液的接触界面上,如果温度较低,如锂离子电池温度低于0℃,其内部的有机电解液会变得更加黏稠甚至凝结。这会阻碍电解液内导电介质的活动,严重时会形成锂枝晶,影响电池的使用寿命并造成安全问题。同时,低温会引起电池内部化学反应速率的下降,电池充电缓慢和困难,使得放电电压平台效应、放电电流和输出功率显著下降,导致电池的性能恶化。
低温还会降低电池内部化学反应的深度,直接减小电池的容量。但是随着温度的逐渐升高,上述不良情况将有所改善,电池内部的化学反应速率随之加快,电解液传递能力增强,化学反应更加彻底,使得输出功率和电池容量会上升。这会延长电池的使用寿命,并提高电池的最高输出电流和放电平台电压。然而,若温度过高,如锂离子电池温度远高于45℃,则会造成电池内部电解液的分解变质,破坏化学平衡,导致一系列不良副反应的发生,缩短电池的使用寿命,并造成很大的安全隐患。
近年来,新能源汽车因为电池温度过高而产生自燃的现象屡见不鲜。因此,使电池始终处于一个适宜的温度区间,对电池的性能和寿命有着至关重要的影响。电池在作为动力电源使用时,往往需要串并联成为电池组,电池在充放电过程中常常产生大量的热量,串并联成组后又产生了新的问题。例如,在锂离子电池组中,不同电池单体的固有物性参数存在一定差异,主要体现在内阻、电压、容量等方面。由于新能源汽车的车载电机在行驶过程中所需电压需要达到300V以上,而锂离子电池的单体电压一般都在3.3~3.6V之间,所以为了满足新能源汽车的使用要求,所需的电池单体数目巨大,甚至可能会达到上百块。
锂离子电池单体在使用时并无过高要求,也不涉及电池间的均一性等问题,进行简单的状态监控即可正常使用。而在锂离子电池组涉及许多个单体电池的协同工作时,使用条件则变得很苛刻。究其原因,主要是同一品牌、同一规格的电池组内,各单体的电压、内阻、容量和温度等性能参数有差异。例如有的电池单体内阻较大,有的较小,有的电池在放电过程中电压下降较快,有的下降则较慢。在充放电的过程中,各单体电池的运行电压会有较大波动,从而导致整个电池组的工作电压不断波动,影响电池组整体电压的稳定性。在这种状态下工作的锂离子电池组内电池的使用寿命会进一步缩短,并且会影响新能源汽车的整体性能。运行工况较复杂时,部分电池可能会因超出合理的温度范围而导致电池着火、爆炸等一系列危险事故。
由于车辆空间有限,电池模块排列紧密,很容易引起电池组内热量的堆积,造成其温度超出最佳工作温度区间,严重影响电池的性能,甚至会直接导致电池的报废。此外,处于不同位置的电池单体对散热条件的要求不尽相同,若不能采取合理的散热结构对其进行热管理,则会导致电池组不同单体之间的温度有所差异。若差异过大,则高温处的电池相比于低温处更易老化,长时间运行时会导致电池组内部各单体性能差异逐步加大,一致性受到较大破坏,最终会因高温区域电池寿命的缩短而导致电池组整体性能的下降以及使用寿命的缩短。因此,为了保证电池组的使用寿命和安全性要求,必须将电池组内各个电池单体的温度和各单体间的温度差异控制在一个合理的温度范围之内,而这一目标的实现离不开设计良好、行之有效的热管理系统。
电池热管理包括散热管理和加热管理两个方面。在保证电池组处于合理工作温度范围之内的同时,也需要均衡电池箱内各点的温度,保持各单体电池的温度一致,防止因温度差异过大而造成电池组整体性能的下降。散热管理最直接的目的是防止电池组的温度过高,即抑制电池组的最大温升;而加热管理主要是为防止电池组在充电过程中因为温度过低而产生的充电缓慢、容量大幅衰减等负面影响。而低温对电池放电阶段则影响不大。通过对大量电池工况数据进行分析,发现电池组在放电过程中常常会因散热不及时而造成高温的情况。锂离子电池的温度区间如图2-4所示。
国内外许多学者根据研究电池种类和形状的不同,提出了各种各样的设计方案,究其原理,主要为风冷、液冷、相变冷却和热管冷却四种方式。其中,风冷经济成本最低;液冷除了需要盛放冷却介质的空间,还需额外的循环系统,相变冷却和热管冷却的方法则较为昂贵。

图2-4 锂离子电池的温度区间
2.3.2 风冷
强迫空气对流冷却法是一种“物美价廉”的冷却方法,如果电池模块周围空间允许,都会安装局部散热器或风扇,还会利用辅助的或汽车自带的蒸发器来提供冷风。该方法对电池的封装设计要求有所降低,可用于较为复杂的系统,电池在车上的位置也不再受限制,从而不影响新能源汽车的通过性。Nissan的铝合金薄膜电池就是采用该方法,进行圆筒形设计并使用风扇冷却。锂离子电池的风冷方法如图2-5所示。

图2-5 锂离子电池的风冷方法
2.3.3 液冷
在相同的流率下,常用的是与模块直接接触的液体(如矿物油),其传热系数比空气高得多,且液体边界层更薄,有更高的热导率。但由于油的黏度较高,需要较高的泵功率,所以通常使用时流率都不高,因此综合分析结果,油的热导率通常只比空气高1.5~3倍;而非直接接触式液体,如水或乙二醇水溶液,黏度比大多数油低,热导率比油高,因此有较高的传热系数。电解流体不仅能显著降低电池过高的温度,还可以使电池模块温度分布比较均匀,使得发出的热以潜热的形式储存起来,在充电或很冷的环境下工作时释放出来,是最有效的散热方式之一。
液体冷却系统主要有被动式液体冷却系统和主动式液体冷却系统。但是液冷方式也有其缺点和不足。主要缺点:采用液冷之后电池组系统的总体质量较大,电池组的结构相对更加复杂,使用中存在漏液的可能,整体装置的维修和保养程序复杂。而新能源汽车的锂离子电池组模块具有成本高、个数多、质量体积都较大等特点。这就要求附加的冷却系统,在不损耗电池本身能量的基础上,尽可能地降低冷却装置的质量,减少冷却装置的额外能耗,实现汽车结构简洁化的要求。同时也必须考虑对锂离子电池及相关通电线路的保护,才能避免在行驶过程中出现漏电、漏液等危险情况,降低电子电路故障的概率,同时提高电池的效率、延长使用寿命。锂离子电池的被动式和主动式液冷分别如图2-6和图2-7所示。

图2-6 锂离子电池的被动式液冷

图2-7 锂离子电池的主动式液冷
2.3.4 相变冷却
相变材料(Phase Change Material,PCM)是一类特殊的功能材料,能在恒温或近似恒温的情况下发生相变,同时吸收或释放大量的热。石蜡的毒性低、价格便宜、单位质量的相变潜热较高、相变温度位于电池安全运行温度范围内,适合用作锂离子电池组热管理的PCM。
目前,主要可采用石蜡与多孔物质相结合、添加高导热系数添加剂的方式,提高石蜡的导热性能。泡沫铜吸附石蜡可用于新能源汽车电池组的热管理,在运行工况发生变化时,电池组的最高温度和最大温差可得到很好的控制。石蜡与石墨片制成的复合材料,具有较高的导热性能和机械强度,应用于电池组热管理,不仅可降低电池组的最高温度和模块间的温差,降低电池组容量衰减率,在寒冷条件下还可对电池组进行持久保温。
向石蜡中添加碳纤维也可提高其导热性能,当碳纤维的长度为2mm、质量分数为0.46%时,电池组的最高温升下降45%。基于PCM的电池热管理系统,结构简单、节省空间、相变潜热大、温度均匀波动较小。但是,PCM冷却技术属于被动冷却,如果不能及时将热量移除,电池组在经历长时间连续充电过程中易引发安全问题。
2.3.5 热管冷却
热管是一种高效的换热元件,具有较高的传热能力,热管进行热传输的核心是利用其管内制冷介质的吸热汽化及放热凝结。与单纯的导热相比,热管传输的热量要大得多,并且热管的结构设计灵活多变,适用于很多行业。自1964年美国的GMGrover发明热管后,热管已在众多换热领域发挥了重要的作用。比如在航空工业,使用热管束来降低飞行器与空气高速摩擦产生的局部高温;在电子工业,使用热管为CPU散热;在能源动力行业,大多数情况下利用热管进行余热回收。热管是一种利用相变进行高效传热的热传导器,封闭空心管内的制冷介质在蒸发段吸收电池热量,然后在冷凝端将热量传递到环境空气中,使电池温度迅速降低。
热管的种类主要分为重力热管、脉动热管及烧结热管等。受限于形状,热管不适合直接与电池接触换热,常焊接在电池间的金属板上。受制冷介质特性的影响,不同的脉动热管适用于不同场合,其中,以水和正戊烷的混合物为制冷介质、填充量为60%的脉动热管,适用于低负荷的热管理;当空气侧温度高于40℃时,以水或甲醇为制冷介质的冷却效果较好。热管形式多样,有助于开发冷却/加热电池热管理系统,保证电池组在高温和0℃以下的环境中,工作在最佳温度范围,确保正常运行。热管安装位置灵活多变,可在热管下方设置空气通道,利用烟囱抽吸效应辅助散热;或在蒸发段处增加翅片,扩大散热面积,热负荷高的时候结合强制风冷。