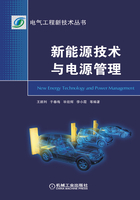
2.2 锂离子电池安全保护
2.2.1 基础安全保护措施
由于锂离子电池的化学特性,在正常使用过程中,其内部进行电能与化学能相互转化的化学正反应,在某些条件下,如对其过充电、过放电或过电流,将会导致电池内部发生化学副反应,该副反应加剧后,严重影响电池的性能与使用寿命,并可能产生大量气体,使电池内部压力迅速增大后爆炸而导致安全问题。因此,所有的锂离子电池都需要一个保护电路,用于对电池的充、放电状态进行有效监测,并在某些条件下关断充、放电回路以防对电池发生损害:
1)充电时不得高于最大门限电压,放电时不得低于最小门限电压。无论任何时间,锂离子电池电压都必须保持在最小门限电压以上,低电压的过放电或自放电反应会导致锂离子活性物质分解破坏,并且不可逆转。
2)锂离子电池任何形式的过充电都可能会导致电池性能受到严重破坏,甚至爆炸,因而在充电过程中,要尽量避免对电池过充电。
3)避免高温。温度过高有缩短寿命、引发爆炸的风险,因此要远离高温热源。
4)避免冻结。多数锂离子电池电解质溶液的冰点为-40℃,低温使得电池性能降低,甚至损害电池。
基于阻抗跟踪技术的电池管理单元(Battery Management Unit,BMU)会在整个电池使用周期内监控单元阻抗和电压失衡,并有可能检测电池的微小短路(Micro-short),防止电池单元造成火灾乃至爆炸。对于锂离子电池包制造商来说,针对电池供电系统构建安全且可靠的产品是至关重要的。电池包中的电池管理电路可以监控锂离子电池的运行状态,包括电池阻抗、温度、单元电压、充电和放电电流以及充电状态等,以为系统提供详细的剩余运转时间和电池健康状况信息,确保系统做出正确的决策。此外,为了改进电池的安全性能,即使只有一种故障发生,例如过电流、短路、单元和电池包的电压过高、温度过高等,系统也会关闭两个和锂离子电池串联的背靠背(Back-to-back)保护MOSFET,将电池单元断开。
2.2.2 锂离子电池安全
过高的工作温度将加速电池的老化,并可能导致锂离子电池包的热失控(Thermal Run-Away)及爆炸。对于锂离子电池高度活性化的含能材料来说,这一点是备受关注的。大电流的过充电及短路都有可能造成电池温度的快速上升。锂离子电池过充电期间,活跃的金属锂沉积在电池的正极,其材料极大地增加了爆炸的危险性。锂离子将有可能与多种材料(包括电解液及负极材料)起反应而爆炸。例如,锂/碳插层混合物与水发生反应,并释放出氢气,氢气有可能被反应放热所引燃;负极材料(诸如LiCoO2),在温度超过175℃的热失控温度限值(4.3V单元电压)时,也将开始与电解液发生反应。
锂离子电池使用很薄的微孔膜(Micro-porous Film)材料(例如聚烯烃),进行电池正负极的电子隔离,因为此类材料具有卓越的力学性能、化学稳定性以及可接受的价格。聚烯烃的熔点范围较低,为135~165℃,使得聚烯烃适用于作为热保险(Fuse)材料。随着温度的升高并达到聚合体的熔点,材料的多孔性将失效,其目的是使锂离子无法在电极之间流动,从而关断电池。同时,热敏陶瓷设备以及安全排出口,为锂离子电池提供了额外的保护。电池的外壳,一般作为负极接线端,通常为典型的镀镍金属板。在壳体密封的情况下,金属微粒将可能污染电池的内部。随着时间的推移,微粒有可能迁移至隔离器,并使得电池正极与负极之间的绝缘层老化。而正极与负极之间的微小短路将允许电子肆意流动,并最终使电池失效。绝大多数情况下,此类失效等同于电池无法供电且功能完全终止。在少数情况下,电池有可能过热、熔断、着火乃至爆炸。这就是近期所报道的电池故障的主要根源,并使得一些厂商不得不将其产品召回。
2.2.3 电池管理单元
电池材料的不断开发提升了热失控的上限温度。另一方面,虽然电池必须通过严格的安全测试,但提供正确的充电状态并很好地应对多种有可能出现的电子元器件故障,仍然是系统设计人员的职责所在。过电压、过电流、短路、过热状态以及外部分立元件的故障都有可能引起电池突变而失效。这就意味着需要采取多重的保护——在同一电池包内具有至少两个独立的保护电路或机制。同时,还希望具备用于检测电池内部微小短路的电子电路,以避免电池故障。电池包内电池管理单元框图如图2-2所示,其组成包括电量计集成电路(Integrated Circuit,IC)、模拟前端电路(Analog Front end Circuit,AFE)和独立的二级安全保护电路。

图2-2 电池管理单元框图
电量计集成电路设计用于精确地指示可用的锂离子电池电量。该电路独特的算法允许实时地追踪电池包的蓄电量变化、电池阻抗、电压、电流、温度以及其他电路信息。电量计自动地计算充电及放电的速率、自放电以及电池单元老化,在电池使用寿命期限内实现了高精度的电量计量。例如,一系列专利的阻抗追踪电量计,包括bq20z70,bq20z80以及bq20z90,均可在电池寿命期限内提供高达1%精度的计量。单个热敏电阻用于监测锂离子电池的温度,以实现电池单元的过热保护,并用于充电及放电限定。例如,电池单元一般不允许在低于0℃或高于45℃的温度范围内充电,且不允许在电池单元温度高于65℃时放电。如检测到过电压、过电流或过热状态,电量计IC将指令控制AFE关闭充电及放电MOSFET V1及V2。当检测到电池欠电压(Under-Voltage)状态时,则将指令控制AFE关闭放电MOSFET V2,且同时保持充电MOSFET V1开启,以允许电池充电。
AFE的主要任务是对过载、短路的检测,并保护充电及放电MOSFET、电池单元以及其他线路上的元件,避免过电流状态。过载检测用于检测电池放电流向上的过电流(Over Current,OC)。同时,短路(Short Circuit,SC)检测用于检测充电及放电流向上的过电流。AFE电路的过载和短路限定以及延迟时间,均可通过电量计的数据闪存编程设定。当检测到过载或短路状态,且达到了程序设定的延迟时间时,充电及放电MOSFET V1及V2将被关闭,详细的状态信息将存储于AFE的状态寄存器中,从而电量计可读取并调查导致故障的原因。
对于计量2个、3个或4个锂离子电池包的电量计芯片集解决方案来说,AFE起了很重要的作用。AFE提供了所需的所有高压接口以及硬件电流保护特性。所提供的I2C兼容接口允许电量计访问AFE寄存器并配置AFE的保护特性。AFE还集成了电池单元平衡控制。多数情况下,在多单元电池包中,每个独立电池单元的荷电状态(SOC)彼此不同,从而导致了不平衡单元间的电压差别。AFE针对每一电池单元整合了旁通通路,可用于降低每一电池单元的充电电流,从而为电池单元充电期间的SOC平衡提供了条件。基于阻抗追踪电量计对每一电池单元化学荷电状态的确定,可在需要单元平衡时做出正确的决策。
具有不同激活时间的多级过电流保护,使得电池保护更为强健。电量计具有两层的充电/放电过电流保护设定,而AFE则提供了第三层的放电过电流保护。在短路状态下,MOSFET及电池可能在数秒内毁坏,电量计芯片集就完全依靠AFE来自动关断MOSFET,以免产生毁坏。多级电池过电流保护如图2-3所示。

图2-3 多级电池过电流保护
当电量计IC及其所关联的AFE提供过电压保护时,电压监测的采样特性限制了此类保护系统的响应时间。绝大多数应用要求能快速响应且实时、独立的过电压监测器,并与电量计、AFE协同运作。该监测器独立于电量计及AFE,监测每一电池单元的电压,并针对每一达到硬件编码过电压限的电池单元提供逻辑电平输出。过电压保护的响应时间取决于外部延迟电容的大小。在典型的应用中,秒量级保护器的输出将触发熔丝或其他失效保护设备,以永久性地将锂离子电池与系统分离。
2.2.4 永久性失效保护
对于电池管理单元来说,很重要的一点是要为非正常状态下的电池包提供趋于保守的关断。永久性失效保护包括过电流的放电及充电故障状态下的安全、过热的放电及充电状态下的安全、过电压的故障状态(峰值电压)以及电池平衡故障、短接放电FET故障、充电时的金属-氧化物半导体场效应晶体管(Metal-Oxide-Semiconductor Field-Effect Transistor,MOSFET)故障状态下的安全。制造商可选择任意组合上述的永久性失效保护。当检测到此类故障时,保护设备将熔断熔丝,以使电池包永久性失效。作为电子元器件故障的外部失效验证,电池管理单元设计用于检测充电及放电MOSFET的失效与否。如果任意充电或放电MOSFET短路,则熔丝也将熔断。
电池内部的微小短路也是导致近期多起电池召回的主要原因。如何检测电池内部的微小短路并防止电池着火乃至爆炸呢?外壳封闭处理过程中,金属微粒及其他杂质有可能污染电池内部,从而引起电池内部的微小短路。内部的微小短路将极大地增大电池的自放电速率,使得开路电压较之正常状态下的电池单元有所降低。阻抗追踪电量计监测开路电压,并从而检测电池单元的非均衡性,避免不同电池单元的开路电压差异超过预先设置的限定值。当出现此类失效时,将产生永久性失效的告警并断开MOSFET,熔丝也可配置为熔断。上述行为将使电池包无法作为供电源,并因此屏蔽了电池包的内部微小短路电池单元,从而防止了灾害的发生。
锂电芯爆炸的原因可能是外部短路、内部短路及过充电,包含电池组内部绝缘设计不良等所引起的短路。因此,对锂离子电池的保护,至少要包含充电电压上限、放电电压下限、电流下限和电流上限。一般在锂离子电池组内,除了锂电芯外,都会有保护电路板或者功能丰富的BMS。内部短路主要是因为分切不良的铜箔与铝箔的毛刺刺穿隔膜,或是由于过充电的原因形成的锂枝状结晶刺穿隔膜。细小极片毛刺会造成微短路,因为毛刺很细,有一定的电阻值,因此,电流不会很大。铜、铝箔毛刺是在生产过程中因为分切不良而造成的,可检测到的现象是电芯自放电太快,大多数情况下可以在后端筛选时检测出来。而且由于毛刺细小,有时会被烧断,使得电池又恢复正常。因此,因毛刺微短路引发爆炸的概率并不高。
内部短路引发的爆炸,主要还是因为过充电。极片上会富集结晶体,并可能导致刺穿点出现并引发微短路。因此,电池温度会逐渐升高,最后高温将电解液汽化。这种情形,无论是温度过高使材料燃烧,还是外壳先被撑破,使空气进去与锂金属发生激烈氧化,都会爆炸。综合以上爆炸的类型,可以将防爆重点放在防止过充电、防止外部短路及提升电芯安全性三方面。其中,防止过充电和防止外部短路属于电子防护,这与电池组系统设计及电池组装有较大关系;提升电芯安全性的重点是化学与结构设计防护,与电池芯的设计与制造过程品质控制有较大关系。
2.2.5 BMS设计规范
电池保护板或BMS硬件冗余设计,可预防因电子元器件失效而引起的整个保护系统失效,通过电池管理系统对过充电、过放电、过电流等分别提供两道安全防护,此外,为了提升BMS的可靠性,电池的BMS产品须经过高温老化处理,具有静电释放(Electro-Static Discharge,ESD)、浪涌防护及防潮防尘这些基本功能。
BMS不但要提供过充电、过放电、过电流保护功能,还要对庞大的电池系统的运行状态进行监控与管理。为了保证电池工作在相同的温度环境下,BMS还要监控所有电芯的工作温度,具备热平衡功能,高效水冷电池模组可将电池工作温度有效控制在(25±2)℃。此外,为了提升车辆电池安全性,BMS集成有落水监测、烟雾监测、碰撞监测、翻车监测、远程报警及自动灭火等安全功能。
锂电芯在生产制造时会严格控制正极、负极、隔膜、电解液等主要原材料的品质,从电芯结构设计到电芯生产制造整个过程,都须经过严格的品质控制与在线检测监控程序,以保证锂电芯的高品质。通过严格的后端筛选与批次的破坏性检验,来保证每一颗出厂电芯的品质都符合品质要求,保证在过充电、过放电、过电流、振动、机械冲击、跌落、挤压、翻转、碰撞、刺穿等情况下,符合品质标准要求。在设计电池系统时,必须对过充电、过放电与过电流分别提供两道电子防护。其中,保护板或BMS是第二道防护,如果没有外部保护,电池发生爆炸就代表设计不良。
2.2.6 锂电芯的品质保障
如果外部保护失败,需要对锂电芯品质提出更高的要求。电池在爆炸前,如果内部有锂原子堆积在材料表面,燃烧爆炸的破坏力会更大。所以锂电芯抗过充电能力比抗外部短路的能力显得更为重要。
电芯抗外部短路的方法,通常包括使用高质量的隔膜纸和采用压力阀两种措施。其中,高质量的隔膜纸效果最好,外部短路时超过99%的电池不会发生爆炸。
2.2.7 提高电池安全性
锂离子电池在热冲击、过充电、过放电和短路等滥用情况下,其内部的活性物质及电解液等组分间将发生化学、电化学反应,产生大量的热量与气体,使得电池内部压力升高,积累到一定程度可能导致电池着火,甚至爆炸。其主要原因如下。
(1)材料热稳定性 锂离子电池在一些滥用情况下,如高阻、过充电、针刺穿透以及挤压等,会导致电极和有机电解液之间的强烈反应,如有机电解液的剧烈氧化、还原或正极分解产生的氧气进一步与有机电解液反应等,这些反应产生的大量热量如不能及时散失到周围环境中,必将导致电池内热失控的产生,最终导致电池的燃烧、爆炸。因此,正负电极、有机电解液相互作用的热稳定性是制约锂离子电池安全性的首要因素。
(2)制造工艺 锂离子电池的制造工艺分为液态和聚合物锂离子电池的制造工艺。无论是何种结构的锂离子电池,电极制造、电池装配等制造过程都会对电池的安全性产生影响。如正极和负极混料、涂布、辊压、裁片或冲切、组装、加注电解液的封口、化成等诸道工序的质量控制,无一不影响电池的性能和安全性。浆料的均匀度决定了活性物质在电极上分布的均匀性,从而影响电池的安全性。浆料细度太大,电池充放电时会出现负极材料膨胀和收缩比较大的变化。可能出现金属锂的析出;浆料细度太小,会导致电池内阻过大。涂布加热温度过低或烘干时间不足,会使溶剂残留,枯结剂部分溶解,造成部分活性物质容易剥离;温度过高,可能造成枯结剂碳化,活性物质脱落形成电池内短路。从提高锂离子电池安全性的角度,可以开展如下几项工作:
1)使用安全型锂离子电池电解质。阻燃电解液是一种功能电解液,这类电解液的阻燃功能通常是通过在常规电解液中加入阻燃添加剂来获得的。阻燃电解液是目前解决锂离子电池燃爆最有效、最经济的方法。使用固体电解质代替有机液态电解质,能够有效提高锂离子电池的安全性。固体电解质包括聚合物固体电解质和无机固体电解质。聚合物电解质,尤其是凝胶型聚合物电解质的研究在近年来取得了很大进展,目前已经成功用于商品化锂离子电池中。干态聚合物电解质由于不像凝胶型聚合物电解质那样包含液态易燃的有机增塑剂,因此不易出现漏液、鼓包和自燃等问题,具有更高的安全性。无机固体电解质具有更好的安全性,不挥发、不燃烧,不存在漏液问题,同时机械强度高,耐热度明显高于液体电解质和有机聚合物,使电池的工作温度范围扩大。将无机材料制成薄膜,更易于实现锂离子电池的小型化,并且这类电池具有超长的储存寿命,能大大拓宽现有锂离子电池的应用领域。
2)提高电极材料的热稳定性。负极材料的热稳定性是由材料结构和充电负极的活性决定的。对于碳材料,如球形碳材料,相对于鳞片状石墨,具有较低的比表面积、较高的充放电平台,所以其充电态活性较小,热稳定性相对较好,安全性高。具有尖晶石结构的Li4Ti5O12,相对于层状石墨的结构稳定性更好,其充放电平台也高得多,因此热稳定性更好,安全性更高。因此,目前对安全性要求更高的动力电池中,通常使用Li4Ti5O12代替普通石墨作为负极。通常负极材料的热稳定性除了材料本身之外,对于同种材料,特别是对石墨来说,负极与电解液界面的固体电解质界面(Solid Electrolyte Interface,SEI)膜的热稳定性更受关注,而这也通常被认为是热失控发生的第一步。
提高SEI膜热稳定性的途径主要有两种:一种是负极材料的表面包覆,如在石墨表面包覆无定形碳或金属层;另一种是在电解液中添加成膜添加剂,在电池活化过程中,它们在电极材料表面形成稳定性较高的SEI膜,有利于获得更好的热稳定性。正极材料和电解液的热反应被认为是热失控发生的主要原因,提高正极材料的热稳定性尤为重要。与负极材料一样,正极材料的本质特征决定了其安全特征。LiFePO4由于具有聚阴离子结构,其中的氧原子非常稳定,受热不易释放,所以不会引起电解液的剧烈反应或燃烧;在过渡金属氧化物中,LiMn2O4在充电态下以MnO2形式存在,由于它的热稳定性较好,所以这种正极材料的相对安全性也较好。此外,也可以通过体相掺杂、表面处理等手段,提高正极材料的热稳定性。