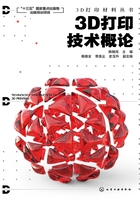
2.4 支撑结构设计
2.4.1 外部支撑结构设计与优化
3D打印,尤其是逐层堆积式3D打印中的一个重要问题就是模型悬空(overhang)问题,即模型在自下至上打印的过程中,由于上层截面大于下层截面,上层截面存在悬空部分,从而可能导致模型崩塌或无法打印的问题。在不改变打印方向的前提下,常用解决方案是在悬空部分添加外部支撑结构。然而,额外的支撑结构不仅难以移除、影响成形表面质量,也耗费材料与时间,因此设计与优化外部支撑结构成为近年来的一个热点研究方向。外部支撑结构的优化目标主要分为最小化支撑结构体积和最优化表面质量两种,根据需求选择最主要目标。
2.4.2 外部支撑结构的添加
打印材料一般具有“黏性”,在一定倾斜角度内的悬空部分可以在打印过程中自支撑,大于可自支撑角度的悬空则需要额外支撑结构,该角度取决于材料本身的性质和打印原理(FDM:约45°;点曝光:90°)。为保证可打印性,保守且简单的方法便是在所有倾斜角度过大的悬空部分以下添加支撑结构。该方法的具体实现以图2-9中的二维树形为例。

图2-9 二维树形的悬空分析
垂直底面向上在打印空间内引射线,这些射线可能与模型相交,记录从下至上进入模型的点处的表面倾斜角度,如果倾斜角度大于可支撑的角度,则该点是需要支撑的。在图2-9的树形中,1点与3点都是需要支撑的点,因此1点以下部分和2点到3点之间都是需要添加支撑的部分。分析这些射线即可得到需添加支撑结构的区域。
但是,单纯从倾斜角度来判断是否需要支撑并不足以涵盖全部情况,如图2-10中圈部分,虽然角度上满足支撑,但模型仍无法打印。除此之外,将全部倾斜角度过大的模型表面点都作为需要支撑的点的做法也会导致过度支撑,带来冗余。

图2-10 通过倾斜角度误判的模型示例
由于打印材料的性质,除了可自支撑的悬空部分无需额外支撑外,也允许倾斜角度超标的小部分悬空存在使模型在打印过程中不坍塌。基于这一性质,在模型的局部最低点添加支撑更为有效,免除了上述方法中的冗余。如在图2-10中圈部分中,只需在菱形的最低点处添加支撑即可实现整个菱形部分模型的支撑。通过这一方法可以大幅减少支撑结构的添加量。
支撑结构不仅可以基于模型设计,也可以结合切片分析。2014年Huang等人[3]提出基于模型切片的模型支撑结构设计方法,如图2-11所示。分析相邻切片之间的支撑关系,将每层切片层中需要支撑的区域进行叠加成一个支撑平面,通过最大覆盖法则在此支撑平面上添加需要支撑的点,再将这些点重新添加回模型的每层切片,模型支撑便添加完毕。基于切片分析支撑结构设计方法的具体算法无需对模型整体进行分析,计算量更少,易于优化支撑结构。该方法既可用于分析外部支撑结构,也可用于壳体模型的内部支撑结构设计。设计模型如图2-11所示。

图2-11 图像空间分层制造算法
为了减少支撑结构的材料消耗并减轻去除支撑结构后的残余材料对模型表面质量的影响,打印方向的选择引起研究者的重视。早在1998年Paul等人就关于层积式制造提出了方向选择的问题,根据支撑结构体积、支撑面积、表面精度等需求决定最终的打印方向。如对于图2-12(a)所示零件,以图2-12(b)所示方向打印可以使支撑结构体积最小化。

图2-12 通过改变打印方向使支撑结构体积最小化
倾向于增强表面质量的支撑结构设计也可以通过改变打印方向实现。2015年,Zhang等人[4]提出一种感知模型,学习样本以获得用户偏好,通过改变模型打印方向重新规划支撑结构位置,使支撑结构位置避开用户感兴趣的模型区域,从而减小了残留对人的直观感受的影响,如图2-13所示。

图2-13 基于用户偏好改变打印方向与支撑位置
2.4.3 外部支撑结构的优化
同样由于材料性质,支撑结构并不需要完全打印为实体,通过等间隔采样,生成柱形等中间镂空形状支撑的优化方法可以大幅减少支撑结构的体积,如图2-14所示。

图2-14 柱形支撑结构
一种树形的支撑结构设计方案于2014年由Schmidt等人[5]提出,如图2-15所示,从一组支撑点开始,自上向下生成提供支持结构的支杆。同时使用分水岭和泊松表面抽样方法来组合以及定义支撑点。通过逆向圆锥的限制合并向下延伸的支杆。当支杆到达地面或地面上一个足够平坦的面时,支杆就会停止延伸。由此产生的树状结构具有很高的空间效率,也可减少支撑材料使用和打印总时间。图2-15(b)使用树形支撑结构打印模型的总时间为3h31min,而图2-15(c)使用传统柱状支撑结构打印模型的总时间为4h33min,可见使用树形支撑结构能够节省打印时间。

图2-15 树形支撑结构设计
基于树形结构的想法,Qiu等人[6]将树形结构与泊松结构相结合,通过打印切片层分析出需要添加支撑的位置角度,结合树形结构的原理生成较传统树形结构更少支撑结构的设计,如图2-16所示。

图2-16 树形-泊松支撑结构设计
受建筑启发,Dumas等人[7]提出由桥(bridge)连接而成的脚手架(scaffold)支撑结构,如图2-17所示。其中利用了FDM拉丝成形瞬间的悬挂效应,使产生的黏力将丝的两端进行固定。通过集中受力点提升可支撑能力,在相同材料使用下可支撑的重量要比树状结构大,且由于与模型连接点少,后处理得到的模型表面也较整洁。

图2-17 由桥构成的脚手架支撑结构与树形支撑结构对比
2.4.4 内部结构设计
3D打印不仅限于制造完全填充的模型,伴随着在保持一定力学性能的前提下尽量减少内部填充的需求,结合力学分析与优化的模型处理成为了近年来的研究热点。目前模型内部支撑结构设计从研究角度来讲基本可以分为三类:基于模型结构分析的方法、基于仿生结构的方法和基于切片分析的方法。基于模型结构分析的方法即利用物理或数学形成的结构为基本结构,将诸如泰森多边形[8]、正12面体[9]等结构进行三维建模优化,得到所需的网格。其优点在于支撑结构易分析、易归纳,但难以找到符合力学规律的结构。基于仿生结构的方法即模仿自然界已有的结构[8,10~14]生成模型支撑结构,其优势在于结构的稳定性。基于切片分析的支撑结构设计方法[3],通过分析相邻切片之间的支撑关系获得其需要支撑的部分,以此为依据设计支撑结构。
2.4.5 基于模型结构分析的设计方法
该类方法从整体上研究结构形式与其受力性能之间的关系,将已知结构进行分析解读并映射在3D打印结构设计中[15,16]。模型设计也是为了实现可打印性,可以从最终的结果来反推并优化模型结构,使模型更加符合实际需要。该类方法重点在支撑结构相关的网格处理与优化,通过完善三维网格以及三角面片达到整体优化效果[17,18]。
2013年,Wang等人[19]参考了建筑中的钢架结构,提出一种内部几何框架外部由表皮包裹的蒙皮结构。算法参考了建筑顶端的钢架结构,意在将模型表示为一个表层薄壁的覆盖、内部钢架支撑的结构,使打印实物所需材料的用量最小化,并且通过计算得到的打印实体能满足一定的应力强度,使受力的稳定性、平衡性及可打印性达到要求,如图2-18所示。此外,采用自适应抽样算法优化几何结构,通过有限元分析,优化拓扑结构,筛去冗余的自支撑点,还生成了内外细杆的优化支撑结构。

图2-18 蒙皮结构计算结果与实际打印物品
2014年,Mueller等人[20]借鉴Wang的框架结构,将模型打印分为框架和蒙皮两部分,提出了一种区别于逐层打印的打印方式,如图2-19所示。通过设计线路直接在三维空间中打印线框而非实心结构,这样在保证外观的前提下大大提升了打印速度。另外由于框架结构可以经由设计打印机路径而完成单线打印进程,进而可以通过设计路径而避免支撑结构的添加,这也可以使打印速度提升。

图2-19 网格线打印方法的过程与结果
Wu等人在2016年提出了一种菱形细胞内填充结构的生成方法[21],从而使合成结构能够自动满足对悬架角和壁厚的制造要求,如图2-20所示。在此方法的框架中可以完全避免额外的内部支持结构。内部基本结构为菱形网格,由输入表面模型构建。从原始稀疏的菱形细胞开始,通过数值优化技术,自适应细分菱形网格来提高目标函数,从而在细胞中添加更多的细胞壁。实验证明了在提高机械刚度和静态稳定性的应用中,该内部支撑结构设计方法的有效性。

图2-20 菱形细胞内填充结构设计过程
此外,Chen等人[9]设计了正十二面体内部支撑结构,并重点分析其网格结构的特点,优化与模型的连接部分,使网格连接稳定强韧。Huang等人[3]从整体网格入手,快速确定模型内外侧,添加多层交错纹理拼接的内部结构并进一步优化网格避免内外层判断失误而导致的丢层错误。Sharf等提出的软最邻近迭代(soft ICP)算法[22],在拥有初始位置的前提下可保证网格的自动拼接,并且网格要有一定重叠区域。
2.4.6 基于仿生结构的设计方法
生物经过长期自然选择得到了可以适应环境的某种结构,例如动物骨骼,其皮质骨可以抵御冲击力,而松质骨可以吸收能量抵御拉伸变形,鸟类的骨骼甚至于可以储存空气进一步增强飞行的能力。该类研究即通过模仿生物以及自然结构并研究其存在的功能原理,将其运用到模型结构当中。基于仿生学的结构设计在医用领域也应用广泛,如利用骨小梁金属(多孔钽)棒植入治疗。
2014年Lu等人[8]提出了一种内部优化的多孔结构的内支撑结构。文章首先分析多种结构并指出内支撑结构打印实体的代价最小,同时提出外观无差异、节省打印材料等参考标准。在给定受力情况下,首先对实体进行有限元受力分析,即可得到物体表面和内部采样点的应力场。然后优化采样点,使用采样点计算其Voronoi图,通过计算划分出子空间。使用两个优化的参数α和β对子空间进行掏空,参数的选择取决于应力点的密集分布程度。其中α表示约束子空间掏空单元的数量,β表示内部掏空的程度。文中的结构参考了材料领域应用的泡沫金属多孔结构,最终实现一个拥有强度-重量比的既轻又坚固的蜂窝状结构,如图2-21所示。

图2-21 多孔结构填充算法实现的内部掏空结构
杨文静等人[14]在2015年利用磷酸钙骨水泥(calcium phosphate cement,CPC)人工骨支架的微孔分布及孔隙率与力学性能的关系,如图2-22所示,设计了3种不同主流道模型并在原始模型的基础上对微孔道进行了细化。分别建立这些具有不同孔隙率的支架结构模型,由陶瓷原料经由3D打印技术进行制造。其结构主要为细胞提供支撑。

图2-22 人工骨支架流道结构设计
2017年,Wu等人[23]受骨结构的启发提出了一种新的内支撑设计法,如图2-23所示。骨合成两种类型的结构,紧凑的皮质骨形成它的外壳,松质骨小梁占据其内部。这个组合的结果是自然优化过程,在此过程中,骨头逐渐适应本身的机械负荷(沃尔夫定律)。可以看出,小梁骨的微观结构沿着主应力方向排列。这种自然的优化组合是轻量级的,具有抵抗性,对力的变化也有很强的鲁棒性。通过这种结构优化,获得了近似刚度优化的多孔结构。这些数值优化的结构形似小梁骨,在材料缺乏和力变化的模型设计中具有重量轻和鲁棒的优点。

图2-23 基于骨骼纹理的内部结构设计
2018年,Mao等人[24]针对现有模型内支撑结构均为单一结构的特点,根据模型不同部分的特点生成混合支撑结构,如图2-24所示。首先通过基于SDF的形状分析和力学分析,将模型分割为类柱状结构(VCol)和非柱状结构(NCol),根据力学特点分别设计基于骨骼肌的支撑结构(muscle fiber structure, MFS)和基于四面体晶状体的支撑结构(tetrahedron crystal structure, TCS)。进一步设计过渡层(transitional layer,TL)和支撑杆,保证相邻区域的连通性并增加支撑强度,分别如图2-24(a)中的第130层(MFS)、第470层(TCS)和第250层(TL)所示。实验结果表明,混合结构的模型强度强于单一结构,与现有最好方法对比,在支撑强度相当时材料消耗最少。

图2-24 基于骨骼肌和四面体晶状体的混合结构设计
随着材料革命与模型分析方法的快速发展,3D打印领域的新技术不断开阔人们的眼界,支撑也在向多元化发展。一方面,结合基本结构、仿生学与力学分析的混合支撑方法在不断提出,代替支撑的模型拆解与拼装方法也开始兴起;另一方面,随着固体粉末材料的出现,未成形的材料本身可成为打印中模型的支撑,完全避免了外部支撑结构的添加及其对模型表面的影响,同时,打印材料也不仅仅局限于一种,诸如使用不溶水的材料打印模型并使用溶水的材料打印支撑结构可以在完成打印后用水完全去除支撑结构不留残余,再比如“4D打印”利用不同材料的不同物理性质使得模型在一定条件下自动变形,生成特定形状而无需支撑。总而言之,3D打印中支撑问题的解决方案日趋丰富,设计者与制造者将受益于更广阔的选择空间。