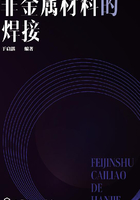
3.3 金刚石与胎体材料的结合
3.3.1 金刚石与胎体的结合形式
金刚石与胎体的结合形式有机械镶嵌、机械包镶与弱化学键结合、稳定的化学键结合等。
(1)机械镶嵌 利用高熔点、高硬度的硬质金属或者化合物,如WC、WC、NbC及氮化物等作为骨架材料,在黏结剂的作用下将金刚石机械地镶嵌在胎体骨架中。这种金刚石制品的加工工艺简单,但是金刚石耗量大,浪费大,成本高。
(2)机械包镶与弱化学键结合 在金刚石表面镀覆(采用电镀、化学镀、真空喷镀等方法)一层极薄的中间金属,如Ni、Cr、Ti等。这些方法大多仍然是在金刚石表面机械地包裹一层金属薄膜,或者少数能够形成很弱的金刚石与包裹金属之间的化学键结合。依靠这种金属与胎体金属的焊接,提高了金刚石与胎体之间的连接强度。但是,工艺过程不是很可靠,有的工艺很复杂,镀覆周期长。
(3)稳定的化学键结合 在金刚石与胎体之间形成稳定的化学键结合,这种稳定的化学键结合就是加入与金刚石(碳)能够发生反应形成碳化物的添加剂,使其在金刚石表面形成一个金属碳化物表面层,使金刚石表面金属化,从而使金刚石具有良好的焊接性,实现金刚石与胎体的直接焊接。这是提高金刚石焊接性的根本途径。
3.3.2 金刚石表面形成金属碳化物
金刚石表面形成金属碳化物是改善金刚石焊接性的主要方法,前面说到的采用在金刚石表面涂镀的方法是其中之一,还可以采取在胎体材料与金刚石之间加入能够形成金属碳化物的材料作为中间层,在烧结过程中在胎体表面形成了金属碳化物包裹在金刚石周围,及将金刚石与能够形成金属碳化物的材料一同加入胎体材料中进行烧结,就在金刚石表面形成了金属碳化物溶入胎体材料中的方法。
(1)采用中间层以形成金属碳化物
①金刚石表面形成金属碳化物的机理和过程。
a.金刚石表面形成金属碳化物的机理。由于金刚石很难被其它物质所润湿,化学稳定性极好,几乎不与酸作用,与碱作用缓慢。但是在高温下,当Te、Co、Ni、Mn、Cr以及铂族金属处于熔化状态时,能够溶解金刚石;另外,如Ti、Zr、V等强碳化物形成元素,在一定的温度和压力下,纯金属能够与其形成金属碳化物。但是,上述金属的表面,在室温下,几乎都覆盖一层氧化物,不能够与金刚石反应形成金属碳化物的。为此,可以将这些金属进行预处理,也就是采用氢化和氮化的方法,使之形成氢化物或氮化物TiH2、Ti3N2、ZrH2、Zr3N2等,在一定的温度和压力下,氢化物和氮化物发生分解,露出纯金属表面与金刚石接触发生反应,形成碳化物TiC、ZrC、VC等金属碳化物表面层;或者形成固溶体,使金刚石与金属之间形成牢固的连接。1958年美国就在Ag-Cu合金中加入TiH2,通过钛实现了金刚石的焊接。
b.金刚石表面形成金属碳化物的过程。为了能够使金刚石表面形成金属碳化物过渡层,采用TiH2、Ti3N2和ZrH2、Zr3N2加入金刚石与胎体金属之间,然后在炉中进行烧结(880~900℃,保温4~5min,压力20MPa)。其碳化物形成过程如下。
ⅰ.当烧结温度达到TiH2、Ti3N2、ZrH2、Zr3N2等的分解温度时,TiH2、Ti3N2、ZrH2、Zr3N2等开始分解:
TiH2[Ti]+H2↑ (3-5)
ZrH2[Zr]+H2↑ (3-6)
这时呈现出的Ti、Zr等纯金属具有很高的活性。
ⅱ.在达到TiH2、Ti3N2、ZrH2、Zr3N2等的分解温度的高温之下,C也具有很高的化学活性,也开始向周围(包括Ti、Zr和胎体)扩散,同时,Ti、Zr等活性元素也向金刚石扩散和渗透。
ⅲ.金刚石表面的C原子与Ti、Zr等形成间隙式固溶体,发生固溶扩散,并且逐步转变为反应扩散。
ⅳ.温度继续升高,这时析出的金属Ti与被激活的金刚石表面的碳原子在298~1150℃下发生如下反应:
Ti+CTiC (3-7)
Zr+CZrC (3-8)
形成的TiC、ZrC包裹着金刚石,从而改善了金刚石的焊接性。图3-37所示为这种反应的示意图,图3-38所示为这个反应过程的物相变化。

图3-37 基体金属与金刚石之间产生的碳化物

图3-38 烧结中反应过程的物相变化
C2—表面有被激活的C原子的金刚石;C3—失去表面C原子形成TiC和ZrC界面过渡层的金刚石;C4—被TiC和ZrC包裹的金刚石
②金刚石表面形成金属碳化物之后对胎体金属抗弯强度的影响。
表3-15列出了加入Ti、Zr及不加入Ti、Zr时金刚石胎体金属抗弯强度。
表3-15 加入Ti、Zr及不加入Ti、Zr时金刚石胎体金属抗弯强度

金刚石表面形成金属碳化物之后对胎体金属抗弯强度的影响如下。
a.在胎体中加入添加剂TiH2、Ti3N2、ZrH2、Zr3N2与同时加入添加剂TiH2、Ti3N2、ZrH2、Zr3N2和金刚石的抗弯强度没有明显的变化,但比单纯的胎体金属有明显的降低。
b.在胎体中加入金刚石和强碳化物形成元素后,胎体抗弯强度比只加入金刚石不加强碳化物形成元素明显提高。
c.加入不同的添加剂,其胎体的抗弯强度也不同。对Ti来说,加入TiH2比加入Ti3N2好;而对Zr来说,加入ZrH2不如加入Zr3N2,总体来说,加入Zr比加入Ti的抗弯强度高。
d.金刚石的粒度和浓度对胎体金属抗弯强度有影响。对Ti来说,粒度在35~40μm和50~60μm,金刚石浓度为45%时的抗弯强度比金刚石浓度为60%时高;对Zr来说,粒度在35~40μm和50~60μm,金刚石浓度为45%时的抗弯强度比金刚石浓度为60%时低。
e.添加Zr3N2和50~60μm的金刚石浓度为45%时的抗弯强度最佳。
③金刚石表面形成金属碳化物过渡层的结构和性能。对经过烧结之后的金刚石表面附近的分析表明,在分别将TiH2和ZrH2加入金刚石与胎体金属之间,然后在炉中进行烧结(880~900℃,保温4~5min,压力20MPa)之后的金刚石表面的成分(质量比)分别为C∶Ti=11.540∶82.667和C∶Zr=6.043∶88.628,即分别形成了TiC和ZrC的金属碳化物过渡层。
由于金属碳化物的脆性较大,因此不应太厚,控制金属碳化物厚度的方法是控制Ti和Zr加入金刚石与胎体金属之间的量,研究结果认为质量分数为0.8%~1.5%比较合适。
④金刚石-金属复合体的性能。金刚石工具,实际上是金刚石及其镶嵌金刚石的胎体的金属复合体(称之为刀头)与工具基体连接起来得到的结构。
a.不同复合体的力学性能。
ⅰ.金刚石-金属复合体的力学性能。以青铜作为胎体材料,掺入浓度为50%的46目的金刚石,采用冷压烧结的方法制成6.5mm×6.5mm×36mm的试样。采用未镀、化学镀和电镀处理的金刚石颗粒,成型压力为65kN/cm2,在氢气保护下进行785℃×2h烧结。烧结后对其进行力学性能测定。抗弯强度测定是在跨距30mm的支架上以三点弯曲的方式加载;冲击韧性测定是使用JB6型冲击试验机,支点距离30mm的情况下得到的。得到的结果在表3-16中给出。
表3-16 金刚石-青铜复合体的力学性能

从表3-16中可以看到,在青铜胎体中加入金刚石之后其抗弯强度和冲击韧性大约只有原来的1/2,这是由于烧结复合体中金刚石颗粒与青铜胎体界面导致的弱化。但是,当金刚石经过表面金属化之后,得到了一定的改善,与未进行表面金属化的金刚石-青铜复合体相比,经过电镀和化学镀处理的金刚石-青铜复合体的抗弯强度和冲击韧性均有所提高。这说明表面金属化以后,金刚石-青铜复合体的力学性能提高了,而且,电镀比化学镀提高得更大。
ⅱ.金刚石-树脂复合体的力学性能。将树脂取代青铜制造的金刚石-树脂复合体的力学性能试验,也采用上述的方法进行,其结果在表3-17中给出。
表3-17 金刚石-树脂复合体的力学性能

从表3-17中同样可以看出上述的现象,只是增加的幅度小些而已。
b.金刚石-金属复合体的耐磨性能。
ⅰ.重磨削时。以青铜为胎体用冷压烧结方法制成浓度50%、直径10mm的试样,在J02磨损试验机上与碳化硅砂轮进行对磨试验,施加30N/cm2的压力,接触点的线速度为110~130cm/s,测出对磨3min前后砂轮和试样的重量,计算磨削效率和磨耗比,其结果见表3-18。
表3-18 重磨削试验结果

ⅱ.磨削时。以青铜为胎体用冷压烧结方法制成的试样,用来磨削石材,磨削时,施加14N/cm2的压力,测定磨削1h前后石材和试样的重量,计算失重、磨削效率和磨耗比,其结果见表3-19。
表3-19 轻磨削试验结果

可以看出,即金刚石表面金属化(镀层后)的耐磨性明显提高。
c.添加剂添加量对金刚石-金属复合体性能的影响。图3-39所示为金刚石-金属复合体的烧结工艺,分为两次升温,第一次850℃,保温之后进行第二次升温,达到950℃,保温之后冷却。

图3-39 金刚石-金属复合体的烧结工艺
ⅰ.添加剂添加量对金刚石-金属复合体力学性能的影响。在金属复合体(胎体)中加入添加剂TiH2 1%~4%时,添加剂添加量对金刚石-金属复合体力学性能的影响如图3-40所示,对金属复合体(胎体)抗弯强度的影响在表3-20中给出。

图3-40 添加剂添加量对金刚石-金属复合体力学性能的影响
表3-20 添加剂TiH2添加量对金属复合体(胎体)强度的影响

添加剂添加量对金刚石-金属复合体力学性能的影响归根结底是对金刚石-金属复合体组织的影响,添加剂TiH2添加量在2%以上时,金刚石-金属复合体(胎体)组织中黑色的金属间化合物太多,金属间化合物一般比较脆,因此,金刚石-金属复合体(胎体)的抗弯强度降低。
ⅱ.添加剂添加量对金刚石-金属复合体反应层厚度的影响。添加剂添加量对金刚石-金属复合体反应层厚也有影响。在添加剂TiH2添加量低于3%时,金刚石-金属复合体界面层的反应层比较致密,而在添加剂TiH2添加量达到4%时,金刚石-金属复合体界面层的反应层厚度达到10μm,金刚石受到较大的腐蚀,反应层也太厚,金刚石-金属复合体(胎体)比较脆,影响结合强度。
(2)采用向胎体材料中同时加入金刚石和碳化物形成金属元素的方法 向胎体材料中同时加入金刚石和碳化物形成金属元素进行热压来研究这种方法在胎体材料中碳化物形成金属元素的行为,分为四种情况:无碳化物形成金属元素的胎体材料;无碳化物形成金属元素加金刚石的胎体材料;有碳化物形成金属元素的胎体材料;有碳化物形成金属元素加金刚石的胎体材料。金刚石浓度为50%,热压温度为950~1050℃,保温时间为5~10min。
①含有碳化物形成金属元素的胎体材料与石墨的黏结行为。表3-21给出了几种胎体材料与石墨界面的剪切强度,可以看到不含碳化物形成元素的Cu-10%Sn-10%Ni与石墨不能黏结,自然也不能与金刚石黏结(因为石墨与金刚石都是C的集合体,只不过结构不同而已)。含W的胎体材料与石墨的剪切强度很低,这是因为W在Cu中的溶解度很低,C在W中的扩散系数也很小,在试验温度下,W和石墨不发生反应。
表3-21 几种胎体材料与石墨界面的剪切强度 MPa

含Ti的胎体材料与石墨在800℃热压时,就已经有一定的黏结强度,在900~1000℃热压时的黏结强度低于含Cr的胎体材料。
Cu-Cr系的胎体材料与石墨的黏结强度比Cu-Ti系高,但是,其熔化温度也比Cu-Ti系高。在Cu-Cr系胎体材料中加入Al可以降低其熔化温度,如在900℃时,Cu-Sn-Ni-Al-Cr与石墨的黏结强度就已经比较高了。
图3-41和图3-42分别为Cu-10%Sn-5%Cr的界面形貌和界面层能谱图。图3-41上部为石墨,下部为胎体材料,中部为界面反应层,厚度约5μm。

图3-41 Cu-10%Sn-5%Cr的界面形貌

图3-42 Cu-10%Sn-5%Cr的界面层能谱图
表3-22为胎体材料与石墨界面层的显微硬度,可见含Ti和Cr的胎体材料与石墨的界面层的硬度与它们的碳化物的显微硬度很接近。
表3-22 胎体材料与石墨界面层的显微硬度 HV

图3-43为Cu-10%Cr胎体中间夹一层石墨片试样热压之后的接头形貌,上、下部为Cu-10%Cr胎体,中间为石墨,界面层厚度约为5μm,图3-44和图3-45分别为界面附近胎体材料和界面层的能谱分析结果。同样可以看到,在界面层存在Cr的富集,而靠近界面的胎体材料的Cr含量降低,说明胎体材料中的Cr扩散到胎体-石墨的界面。图3-46为Cu-10%Cr胎体与石墨在1050℃之下保温20min的界面层X射线衍射试验的结果。

图3-43 Cu-10%Cr胎体中间夹一层石墨片试样热压之后的接头形貌

图3-44 界面附近胎体材料能谱分析结果

图3-45 界面层的能谱分析结果

图3-46 Cu-10%Cr胎体与石墨在1050℃之下保温20min的界面层X射线衍射试验的结果
不含碳化物形成元素的Cu-10%Sn-10%Ni-10%W胎体与石墨经过热压之后,没有发现碳化物层。也就是说,胎体与石墨没有发生界面反应。
②含有碳化物形成金属元素的胎体材料与金刚石的黏结行为。表3-23给出了胎体材料中有、无碳化物形成金属元素与金刚石的黏结行为。
表3-23 胎体材料中有、无碳化物形成金属元素与金刚石的黏结行为

注:D表示碳化物。
3.3.3 胎体材料与金刚石的界面反应
(1)胎体材料组元在金刚石界面上的分布 对于胎体材料为Cu-Sn、Cu-Ag和Cu-Sn-Zn等(不含碳化物形成元素)时,胎体材料组元的任一元素在金刚石界面上的浓度分布都是均匀的,没有任何偏析。但是,对于含有碳化物形成元素的胎体材料,在与金刚石的界面上就会发生偏析。
图3-47给出了Cu-Sn-Ti合金胎体材料在两颗金刚石之间的各元素的分布,两颗金刚石间距为100m。可以看到,Ti在胎体材料与两颗金刚石的界面上发生了极大的集聚。由于Ti在胎体材料与两颗金刚石的界面上发生了集聚,Cu就在两颗金刚石中间产生了富集,而Sn在富Ti的Cu合金中的溶解,也出现了两个峰值。Cu和Sn分布的变化完全是由于Ti向胎体材料与金刚石界面偏析造成的。

图3-47 Cu-Sn-Ti合金胎体材料在两颗金刚石之间的各元素的分布
图3-48为Cu-15%Ti合金胎体材料与金刚石界面上Ti的分布,图3-49为Cu-15%Si合金胎体材料与金刚石界面上Si的分布,可以看到,与Ti相比,Si只是在金刚石界面附近有偏析,这是由于Si没有Ti的活度大的结果。Si虽然也能够形成硅的碳化物SiC,但是,Ti是强碳化物形成元素,Ti与C的反应比Si与C的反应要激烈得多。

图3-48 Cu-15%Ti合金胎体材料与金刚石界面上Ti的分布

图3-49 Cu-15%Si合金胎体材料与金刚石界面上Si的分布
图3-50给出了Ag-Cu-Cr合金胎体材料与金刚石界面上Cr的分布。Cr也是强碳化物形成元素,可以看到,Cr与C的界面反应也是很激烈的。

图3-50 Ag-Cu-Cr合金胎体材料与金刚石界面上Cr的分布
(2)胎体材料Cu-15%Ti与金刚石的界面反应
①胎体材料Cu-15%Ti的组织。图3-51给出了胎体材料Cu-15%Ti的组织的背散射图像,能谱分析表明,Y区的Ti含量为0.85%,它是α-Cu固溶体;G区的Ti含量为36.4%,它是Ti2Cu3(Ti2Cu3的Ti含量为33.4%)。
②胎体材料Cu-15%Ti与金刚石的界面反应。由于石墨和金刚石均为碳的集合体,只是结构不同而已,它们的化学性能是一样的。图3-52给出了胎体材料Cu-15%Ti与石墨经过加热1200℃保温240min的界面照片。在石墨界面上形成了约5μm的TiC层。这个TiC层的硬度大于1740HV,胎体材料Cu-15%Ti基体组织的硬度为120~280HV。

图3-51 胎体材料Cu-15%Ti的组织的背散射图像

图3-52 胎体材料Cu-15%Ti与石墨经过加热1200℃保温240min的界面照片
在石墨界面不同距离上的X射线结构分析的结果:与石墨界面的距离为35μm,主要是Cu和富铜合金Cu3Ti,与石墨界面的距离为8μm,开始出现TiC,与石墨界面的距离为3μm,TiC大量出现。因此,可以确定,胎体材料Cu-15%Ti与金刚石(石墨)的界面反应的结果,是在与金刚石(石墨)表面不同的距离上产生了不同量钛的碳化物TiC,在金刚石(石墨)表面上完全是TiC,随着与金刚石(石墨)表面距离的增大,TiC逐渐减少,而胎体材料Cu-15%Ti基体组织Cu和富铜合金Cu3Ti就增多。